Introduction
At a manufacturing company in Shah Alam, Malaysia, enhancing the reliability and safety of their electrical systems was a priority. The company aimed to implement a more effective maintenance strategy to proactively identify and address potential electrical issues. Recognizing the importance of preventive maintenance, they sought the expertise of AMKA Technologies Sdn Bhd to conduct comprehensive thermographic inspections. This initiative was designed to detect early signs of electrical faults and improve overall system performance, ensuring operational efficiency and safety.
Project Description
Technicians conducted qualitative assessments by visually inspecting equipment for signs of wear and tear, including discoloration, dust accumulation, and physical damage. They also used the thermal camera to capture infrared images, revealing temperature variations and identifying hotspots that could indicate underlying problems.
Methodology
Inspection Process
Thermal Camera: FLIR T420 thermal camera.
Operating Conditions: Conducted during peak operational hours.
Preparation: The inspection was meticulously scheduled, ensuring all safety protocols were in place.
Scanning: Electrical panels, transformers, switchgear, and motor control centers were systematically scanned using the thermal camera.
Data Collection: Thermal images and temperature readings were captured and recorded.
Qualitative Inspection Overview
The thermographic inspection was carried out with a qualitative approach, focusing on visual patterns and anomalies in the thermal images. By interpreting these patterns, the inspection team could identify areas of concern such as hot spots, indicating potential issues like loose connections, overloads, and insulation breakdowns.
Severity Classification
Direct Method: This method involves aiming the thermal camera directly at the failure point where a direct line of sight is possible.
Severity Categories:
Severity Category
|
Temperature Difference (ΔT)
|
Recommended Action
|
ΔT between similar components
|
ΔT over ambient temperature
|
Continuous Monitoring
|
<1 °C
|
<1 °C
|
No anomalies detected during scanning; no action required.
|
Low Alarm
|
1 – 5 °C
|
1 – 10 °C
|
Anomalies that warrant monitoring; check-up at the next convenient opportunity.
|
High Alarm
|
6 – 15 °C
|
11 – 40 °C
|
Serious anomalies that demand attention soon; repair at scheduled shut down.
|
Danger
|
>15 °C
|
> 40 °C
|
Very serious anomalies necessitating immediate action to prevent imminent failure or hazard.
|
Indirect Method: Used when direct assessment isn't possible due to physical barriers, involving temperature measurements of accessible surfaces to infer the condition of concealed components.
Findings
Thermogram 1: Plastic Injection Area
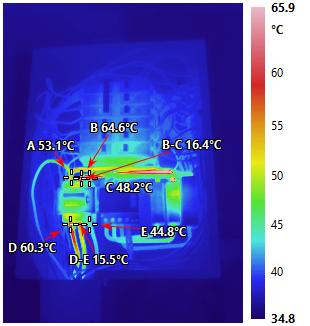
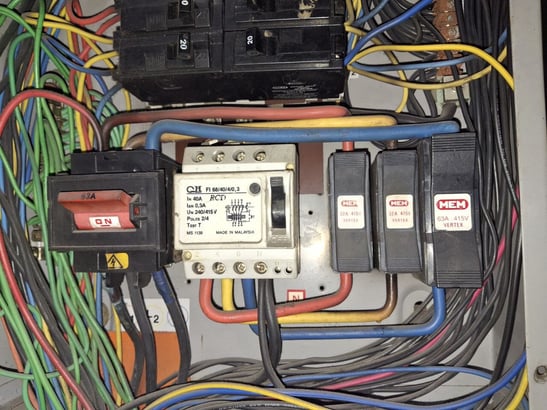
Analysis:
In the Plastic Injection area, our thermographic inspection revealed multiple anomalies in the distribution board. At Spot B, we detected an unbalanced load at phase B with a ΔT of over 15°C higher than similar components, indicating a severe anomaly. Additionally, at Spot D, we identified a loose connection at phase A with a significant temperature difference. These issues posed significant risks, including resistance heating and potential arcing, which could lead to a serious fire hazard. Given the undersized nature of the existing distribution board, an upgrade from 40A to 63A was deemed necessary to handle the electrical load more effectively and prevent overheating.
Recommendation:
Immediate action was recommended to upgrade the distribution board from 40A to 63A due to the existing undersized DB. This upgrade would address both the unbalanced load and the loose connection issues, ensuring safer and more reliable operation.
Thermogram 2: Die Cast Area
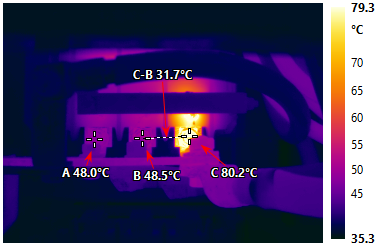
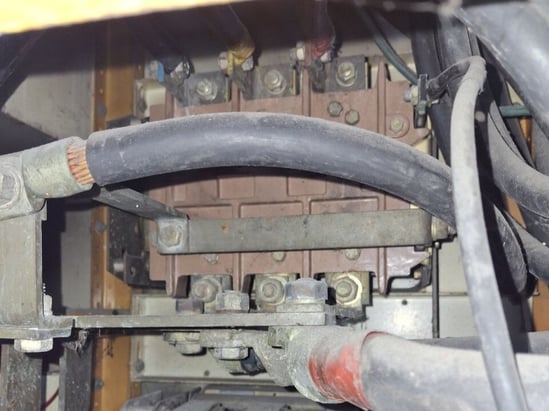
Analysis:
In the Die Cast area, our inspection identified a critical hotspot at Spot C on the breaker, with a ΔT of 31.7°C compared to similar components. This hotspot was indicative of a loose or deteriorated connection. Such a significant temperature rise suggested an imminent risk of failure, which could disrupt operations and potentially cause damage to the equipment.
Recommendation:
To address this issue, we recommended immediate servicing of the breaker, tightening of the terminal, and a thorough check of the fuse holder. These actions were necessary to prevent potential equipment failure and ensure the safety and reliability of the electrical system.
Thermogram 3: Compressor Room
-
Location: COMPRESSOR ROOM
-
Equipment: Isolator switch
-
Severity Category: Danger
-
Infrared Image:
Analysis:
In the Compressor Room, we detected a severe hotspot at Spot C on the isolator switch, with a ΔT of 18.7°C compared to similar components. This thermal anomaly was attributed to visible deteriorated connection. The compromised connection was critical because it could lead to single phasing, a condition where one phase of the power supply is lost. This would cause the 3-phase motor to overheat and eventually fail, jeopardizing the continuous operation of the compressor.
Recommendation:
We recommended immediate corrective action to repair the visible deteriorated terminal or connection. Ensuring the integrity of the connection was crucial to maintaining the compressor's operation and preventing potential damage to the motor.
Actions Taken
Identified Issues:
-
Loose connections
-
Overloaded circuits
-
Insulation failures
Implemented Solutions:
-
-
Tightened Connections: All identified loose connections were tightened to prevent resistance heating and potential arcing.
-
Redistributed Loads: Electrical loads were balanced across circuits to mitigate the risk of overheating and potential circuit failures.
-
Replaced Insulation: Faulty insulation materials were replaced to restore the integrity of the electrical system and prevent future failures.
Implementation Process:
AMKA Technologies coordinated with the company’s maintenance team to implement the solutions without disrupting operations. The corrective actions were carried out during scheduled maintenance windows to minimize downtime.
Results
Outcomes:
-
Improved Reliability: The thermographic inspections and subsequent repairs enhanced the reliability of the electrical systems, reducing the likelihood of unexpected failures.
-
Increased Efficiency: By addressing issues such as loose connections and overloaded circuits, the efficiency of the electrical systems was significantly improved.
-
Enhanced Safety: The proactive identification and correction of electrical faults reduced the risk of electrical fires and other safety hazards.
Benefits:
-
Reduced Equipment Downtime: Regular thermographic inspections and prompt repairs minimized unplanned downtime, ensuring smoother operations.
-
Increased Safety: Improved detection and mitigation of electrical issues enhanced the safety of the workplace, protecting both personnel and equipment.
-
Cost Savings: Preventive maintenance and early fault detection helped avoid costly emergency repairs and extended the lifespan of electrical assets.
Conclusion
The manufacturing company in Shah Alam successfully enhanced the safety and reliability of their electrical systems through comprehensive thermographic inspections conducted by AMKA Technologies. By adopting a proactive maintenance strategy, the company was able to identify and address potential issues early, resulting in improved operational efficiency, increased safety, and significant cost savings.
For more information on thermographic inspections and how they can benefit your operations, contact us today. Get a free quote or schedule a consultation with our experts to ensure your electrical systems operate safely and efficiently.